The Concorde Sculpture
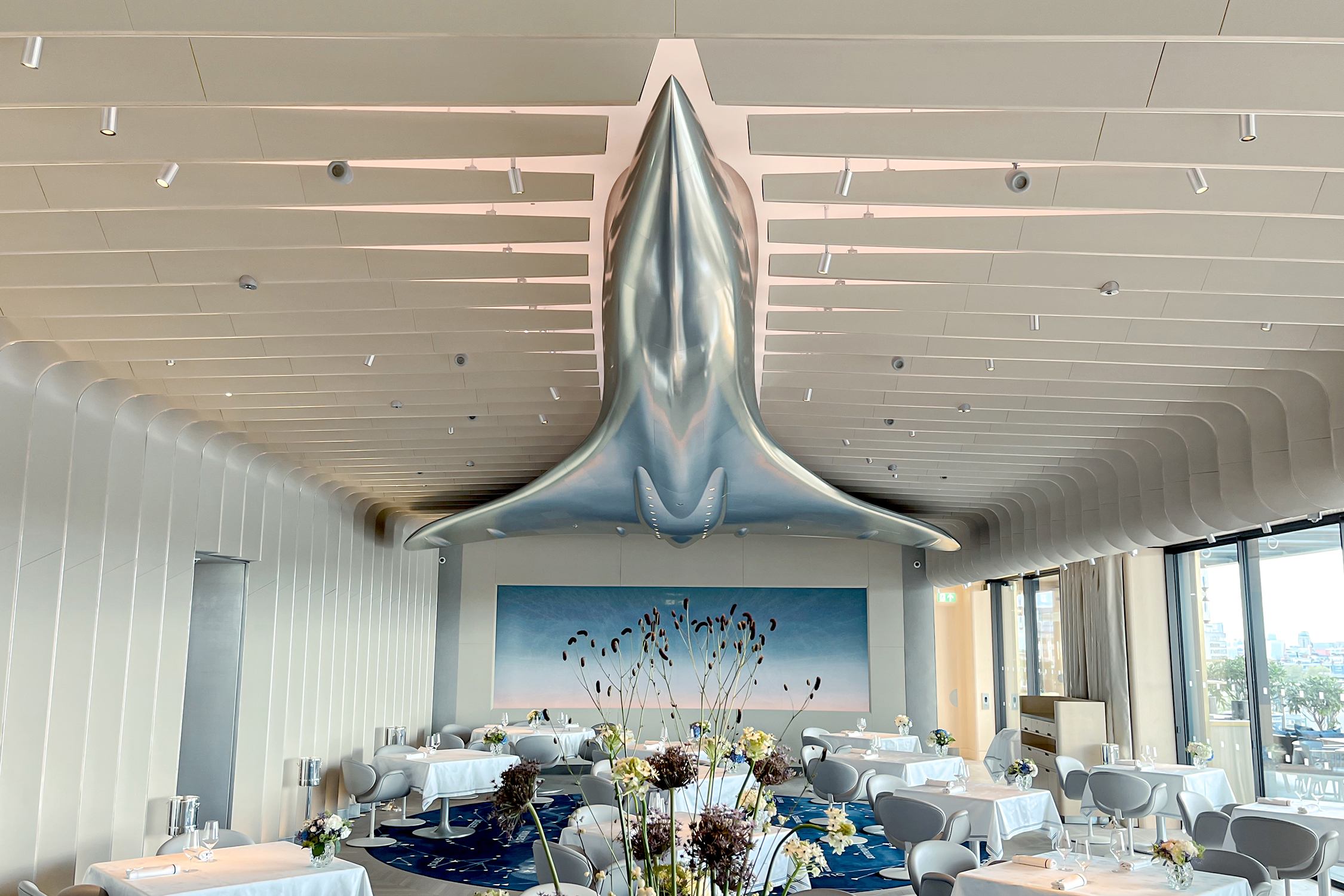
In 2023, our team of three saw the completion of our largest and most innovative project to date: the designing, manufacturing, transportation, and installation of an 11,420-component and 48-foot-long sculpture of the Concorde supersonic airliner that is now suspended from the ceiling of the Brooklands Lounge in London's Peninsula Hotel. The project took nearly five years from the initial concept phase to the completion of manufacturing, and two weeks of on-site work at the hotel to assemble, lift, and install the model aircraft.
The five-year journey of creating the Concorde sculpture was a masterclass in innovation from our small team. Not only was the magnitude of this undertaking beyond anything we’d ever experienced, but the entire project lacked the reassurance of a clearly defined process—the very thing that many design firms depend on. To this point, the client had the means to choose any firm of any size from anywhere in the world, and yet they trusted our small team from South Carolina to execute. In many ways, our size is our advantage. We’re agile and live and die by the success of every project we take on.
During this marathon project, our team’s mantra of “we make what if real” was repeatedly pushed to the limits. From day one, the hotel was actively under construction and to complete our installation was akin to putting the wheels on an already-moving train. The lounge was designed with a Concorde in mind but no blueprints for its design nor its installation had been created until we took the reins. We then simultaneously forward and reverse-engineered the sculpture, working with the architect and contractors in order to account for the necessary infrastructure to support a plane that did not yet exist. We were faced with the challenge of navigating an engineering no man’s land, creating new methods and ideas to overcome a myriad of unforeseeable obstacles.
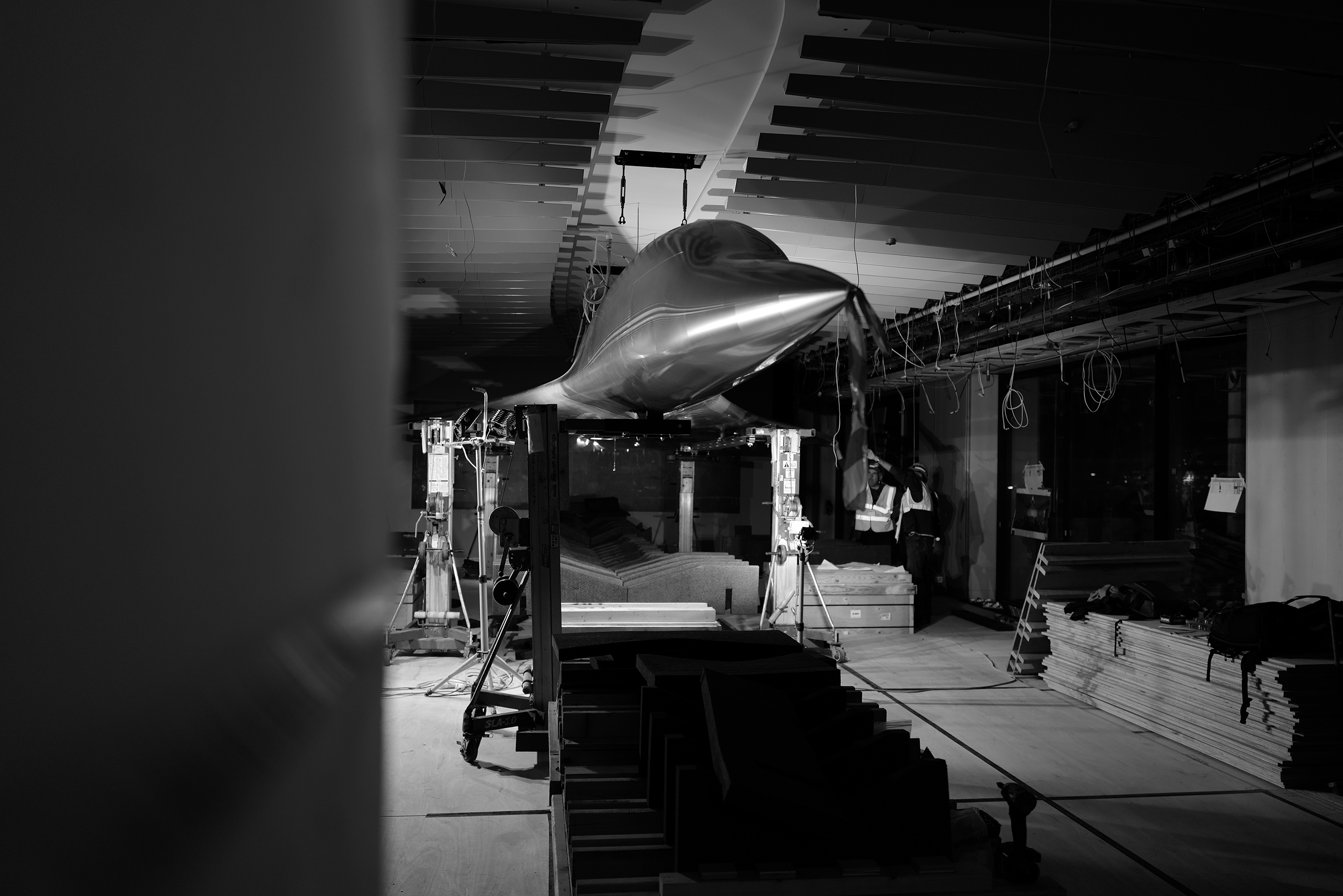
It all began for us in July 2018 when we were told a potential client—the Peninsula Hotel group—was looking for designs for a Concorde lounge. Assuming this meant a Concorde-themed lounge, we quickly rendered an upscale model room that featured paneled walls similar to the panels used throughout the body of the actual aircraft. Much to our surprise, the client countered by clarifying their expectations: A metal Concorde. In full flight. In the ceiling.
It was immediately clear that this project was going to be on a scale unlike anything we’ve ever tackled before. However, daunting challenges happen to be our specialty and so, we accepted the project. The next month, we machined a 3ft aluminum maquette and presented it to the hotel group. They approved. Thus began a two-year courting period involving countless meetings and negotiations before the contract was in place.
It took less than a week for our Head of Design, Kevin Coss, to complete the initial Concorde design. Working in tangent with our founder and CEO, Neil Ferrier, Kevin was able to sketch and render a near-perfect model of the airliner—but with some minor improvements for the purpose of bettering the aesthetics and making the Concorde a piece of sculptural art that's fit for the 5-star hotel. The architect overseeing the design of the lounge wanted the aircraft to feel as if it were cutting through the ceiling in full flight. The final sculpture is what could be considered a “speedform,” something that’s commonly part of the early phases of car design, where the designer works on ideal proportions and surface design before details are added in. Elevated to be the final form in itself, the speedform is the materialization of supersonic flight.
After the completion of the design phase, Neil and our Head of Product, Jeremy Hadden, took the rendered design and pushed it into the production phase. Here we looped in Neal Feay, masters of aluminum machining, to act as our partner in the manufacturing of the aircraft. The hotel group and architects were also heavily present throughout the entire process as designing and producing such a massive piece of art required meeting an equally massive amount of building and safety codes.
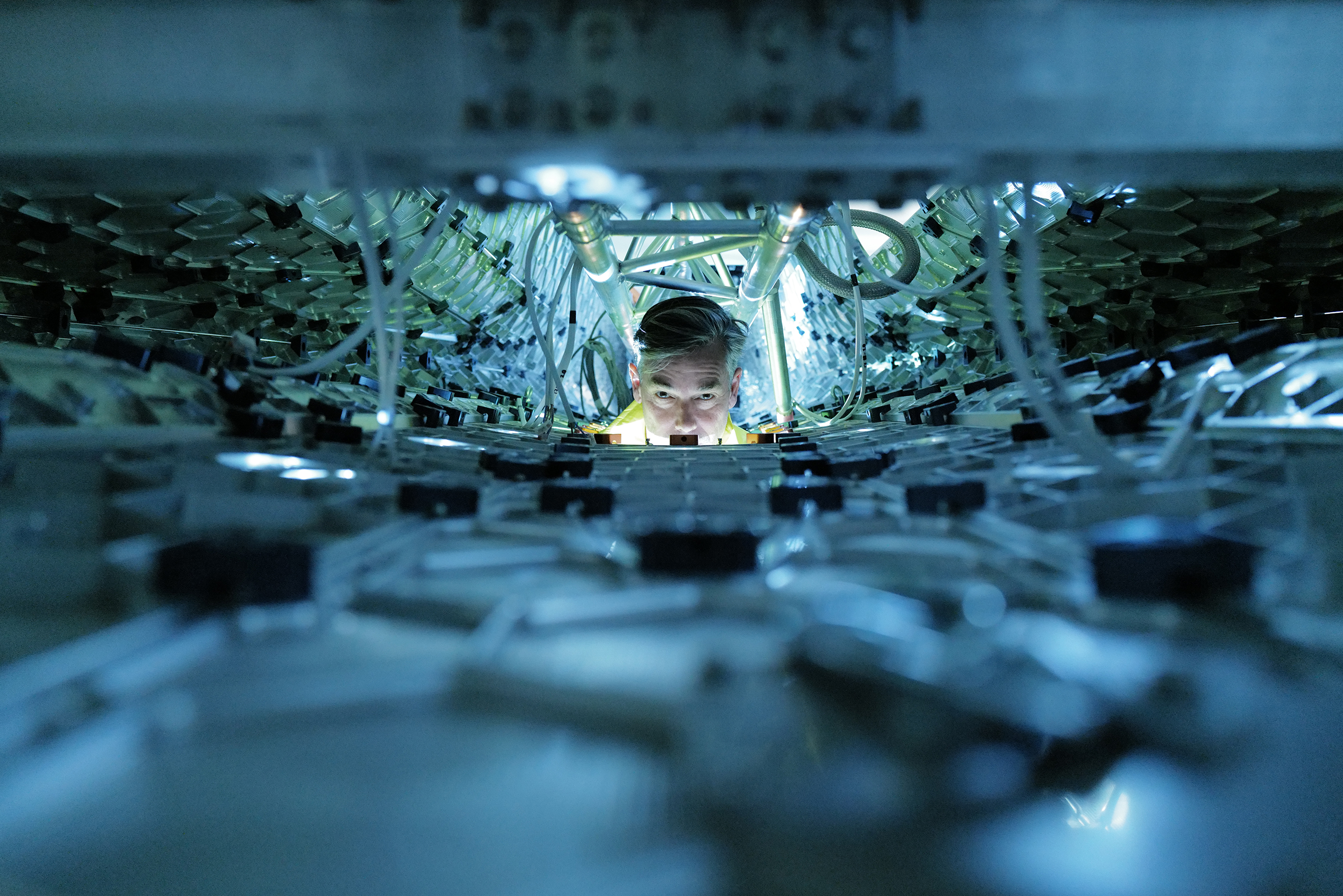
Experience has shown us that you can typically expect the size of the project to dictate the size of its accompanying challenges, and this was no exception. Endlessly we were forced to rethink certain aspects of the sculpture in order to accommodate certain safety guidelines and changing aspects of the room, such as the installation of 24 lights and two sprinklers within the body of the sculpture itself.
Once manufacturing was complete, the real challenges came in London. The Concorde was the final component of the lounge to be assembled, meaning we would be working on multi-million dollar floors for the final assembly and install. Planning to avoid an aircraft-shaped indentation was task number one. Then there was the issue of getting the Concorde in its disassembled state to the Brookland's Lounge. The hotel does not have any freight elevators so the entirety of the aircraft had to be organized in crates that were then lifted by cranes to the level of the lounge. The issue of lifting the Concorde to the ceiling was solved by using scissor lifts, machines that had to be brought in through the windows also via cranes. Once to the ceiling, the craft was then suspended from four sets of resin concrete anchors.
In total, the model Concorde is comprised of 420 machined panels of billet aluminum that are held together by 3,000 patented tension cleats and 8,000 bolts, all together weighing roughly 2,700 pounds.
Discommon stands for Disruptive and Uncommon and our mission is to Make Ordinary Obsolete. We put our soul into every piece that bears our fingerprints, keenly aware that the things we produce could—and should—be passed down through the generations. As a small firm fighting for recognition in a crowded industry, we’re proud that this potentially career-defining piece will hang for years to come as a resounding answer to the question, what if?
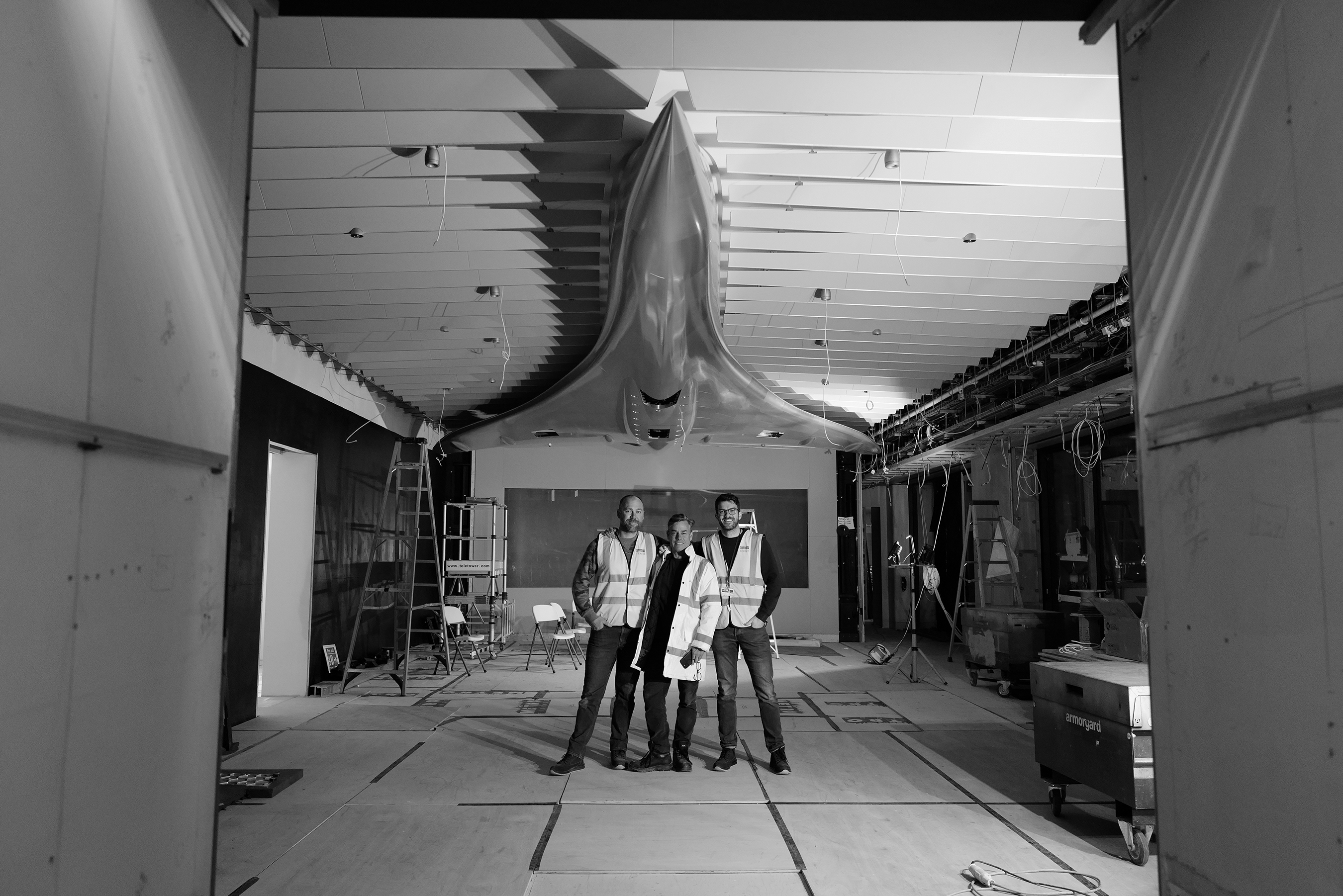
neil@discommon.com
Discommon
324 Wade Hampton Blvd
Greenville, SC 29609
Website by Penta Studio